Who is responsible for determining weld size?
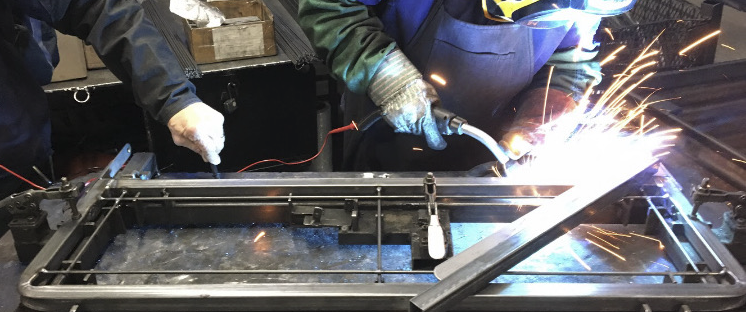
Who determines what size a weld should be? This is a question we ask many of our customers. And we never seem to get a straight answer. In a perfect world, the design engineer should specify all weld sizes and clearly communicate this through welding symbols on the print. But that is hardly ever the […]